He tried to 3D print a Canyon Aeroad bike in four days. It was a disaster—so Canyon sent him a real one instead
'There is so much more engineering that goes into bikes than people think. I think bikes have been around for so long we take them for granted,' discovered Kevin Frias

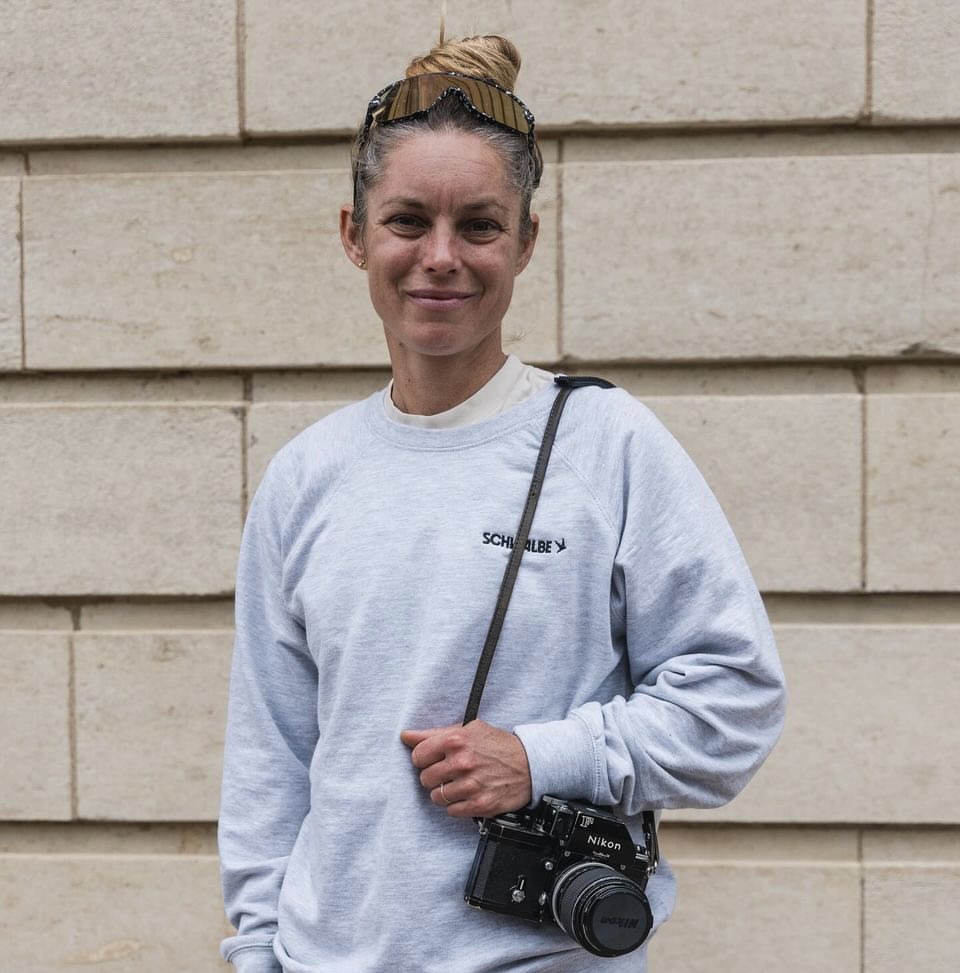
There’s a reason why a brand-new Canyon Aeroad CF SLX 8 Di2 costs more than $6,000. Designing and engineering a high-performance bike takes years of research, development and investment. It’s not a process that happens overnight—or even in a month. But that didn’t stop Kevin Frias of Minneapolis, Minnesota, from attempting to engineer and 3D print his own version of the Canyon Aeroad in less than a week—just in time for his birthday.
“Technology of 3D printing is insane. There are so many models now. You don’t need to know how to design. You can just go download something, buy the filament and then 4 hours later, you have this cool super complex thing,” he told Cycling Weekly.
Frias isn’t new to engineering. He holds a degree in industrial engineering and spent six years working for a major manufacturer. But 18 months ago, he left that career behind to pursue content creation instead, focusing on the bike world. He travels far and wide to ride⸺most recently spending 10 days exploring the Dominican Republic on a borrowed bike to visit his parents.
Back in Minnesota, Frias didn’t have a road bike and he wanted that to change before his birthday on March 31. But rather than buying one, he devised an idea to print one, at home, with a Bambu Lab A1 3D printer he’d purchased just a month earlier.
“I looked it up and no one had ever made a bike. Let me try. I don’t know how hard it’s going to be,” Frias recalled. His bike of choice? The Canyon Aeroad—his dream ride.
Like many bold projects, Frias didn’t waste much time on learning or planning. He just dove right in.
“All of Monday I spent learning 3D modeling, and then at 7 p.m., I was like, let me try to tackle a handlebar,” he shared. With just four days before his birthday, “Project #birthdaybike” was born.
Get The Leadout Newsletter
The latest race content, interviews, features, reviews and expert buying guides, direct to your inbox!
Project Birthday Bike
The real deal
Frias pulled the specifications for the Aeroad straight from Canyon’s website and began designing, with low expectations that anything would actually work. In his first video documenting the process, Frias wrote, “the blowup likely to result from this should encourage you to BUY one of [Canyon’s] amazing bikes.”
Using over 6 kilograms of PLA (plastic) and TPU (rubber) filament, Frias began printing the frame in segments. Why plastics instead of carbon fibre? “The carbon fibre filaments are really, really expensive,” Frias stated.
The process was far from smooth. One printing mishap ruined an entire spool of filament intended for the rear triangle. Another small miscalculation of the fork’s internal width nearly derailed the project again. The experience highlighted the complexities of engineering a bike.
“There is so much more engineering that goes into bikes than people think. I think bikes have been around for so long we take them for granted,” Frias said. “The amount of work or design that goes into improving something .0001% is insane.”
Another major takeaway of this project was witnessing how bikes bring people together. “It’s cool to see how people who aren’t serious cyclists just wanted to see [the project] because they have this affinity towards a bike,” Frias said. Whether it’s a first bike or a first ride, that shared experience brought people together.
As the view count on his Instagram videos started moving into the millions, strangers began reaching out to Frias offering support. When Frias realised he wouldn’t have enough time to complete all the printing on his own, local community members stepped in. Five people volunteered their 3D printers to help, and together, Frias estimates they logged more than 250 cumulative hours of print time.
There’s nothing practical about 3D printing a bike at home. The process involves printing dozens of small, fragile parts that somehow need to fit together like a jigsaw puzzle or with the aid of rods and glue. And the weight of the filament alone is significantly heavier than a real bike.
“It’s exponentially heavier than the real one. One wheel from the 3D printed bike weighs more than the real complete bike,” Frias shared.
Assembling the bike took the better part of a day. Frias began by dry-fitting the parts, then moved on to sanding, drilling holes for reinforcing rods, and gluing everything together. It was a painstaking process in which nothing went as planned. So many of the parts cracked or broke along the way that Frias almost gave up. But he persevered.
By the end, the bike had six cracks in the wheels, five in the frame, no way to mount a saddle, no chain, a front wheel that wouldn’t spin, handlebars that couldn’t be trusted—and none of it could support even the slightest bit of weight.
Frias, however, was far from disappointed.
“I made this!” he exclaimed. “Even though this bike was broken everywhere, I'm glad I finished putting it together.”
Kevin Frias with his 3D printed Canyon Aeroad model
Far from being a failure, the project turned out better than Frias could have imagined. Not only did he bring to life a concept no one had attempted before, but his efforts also caught the attention of Canyon—who surprised him with the real deal: a Canyon Aeroad CF SLX 8 Di2.
“Honestly, Kevin’s inspired us all with his love for cycling, his design prowess, his initiative, and his sheer joy in taking on a really tough project,” Devin Riley, Canyon Bicycles’ Vice President of Marketing and Sales, told Cyling Weekly. “That his dream bike is a Canyon Aeroad puts a smile on our face too, at least as big as his.”
As soon as Canyon discovered Frias’ project, brand representatives reached out to offer support.
“We helped a little, but this was his project through and through and he truly impressed us all,” Riley said. “While he’s creatively demonstrating that the technology’s not quite there yet in terms of 3D printing your own bike, it’s a powerful design tool and who knows where it will take us in the near future. Wherever that is, passionate people like Kevin will no doubt be the ones showing us the way.”
Thank you for reading 20 articles this month* Join now for unlimited access
Enjoy your first month for just £1 / $1 / €1
*Read 5 free articles per month without a subscription
Join now for unlimited access
Try first month for just £1 / $1 / €1
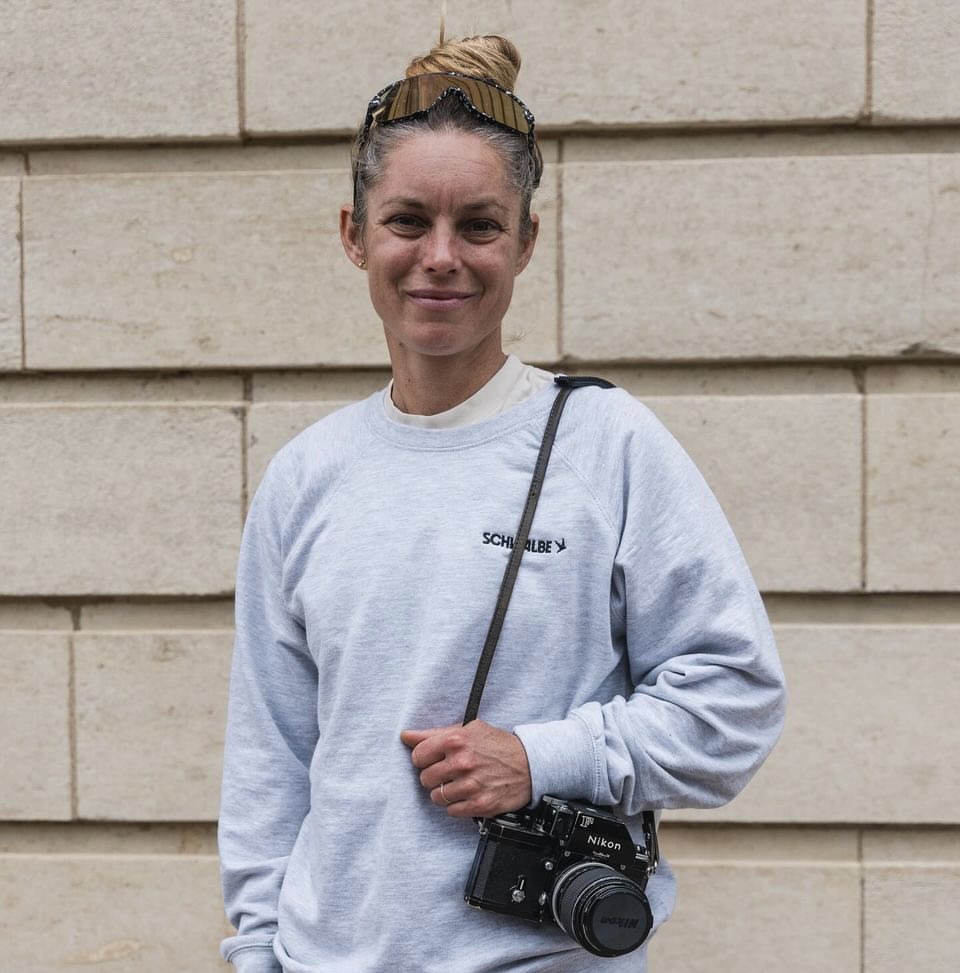
Caroline Dezendorf is an elite off-road cyclist and storyteller with a passion for building community and protecting wild spaces. She lives in Truckee, California, where her backyard is the expansive Sierra Nevada mountains. You can often find her in the mountains, exploring by two wheels or two feet. She aims to inspire future generations to explore the natural world and push beyond their comfort zones.
You must confirm your public display name before commenting
Please logout and then login again, you will then be prompted to enter your display name.
-
Pauline Ferrand-Prevot takes a sensational home victory in Paris-Roubaix
Frenchwoman wins her Hell of the North debut as Letizia Borghesi takes second place and Lorena Wiebes is third
By Peter Cossins Published
-
'It's the only race I’m a bit scared of' - Jack-Rootkin Gray on his Paris-Roubaix debut
22-year-old is in his second year with EF Education-EasyPost after making the move up the pyramid from Saint Piran
By Tom Thewlis Published