How Hutchinson makes its bicycle tyres
Research into new compound formulations is followed by industrial production
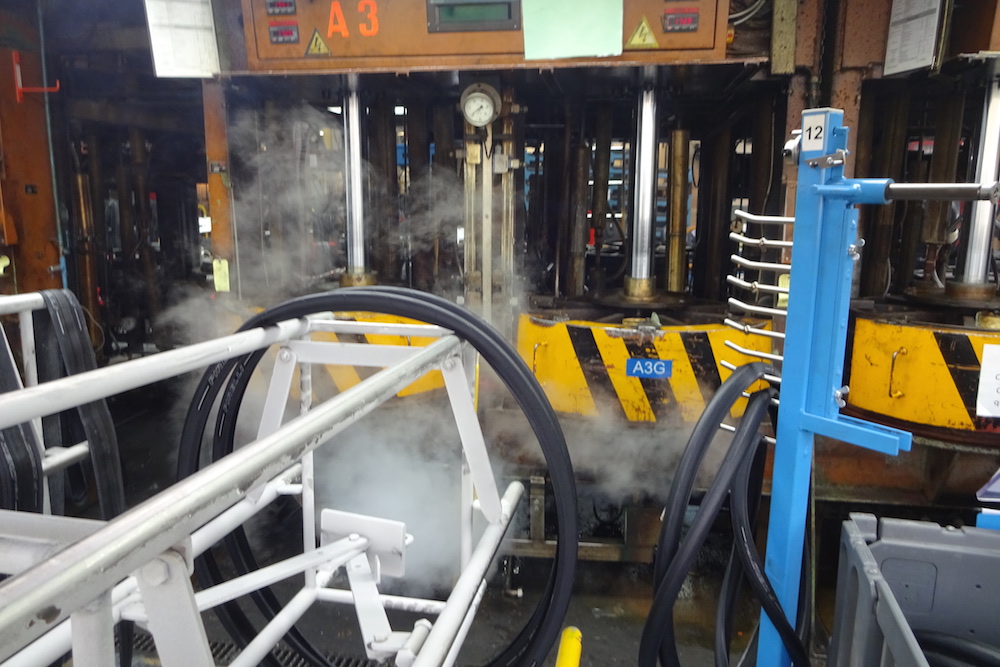

For a French company, Hutchinson has a very Anglo-Saxon sounding name. That’s because the company was set up in 1853 by US businessman Hiram Hutchinson. Attracted by the grants offered by Napoleon III, Hutchinson moved his rubber making machines from the US to set up in Montargis, around 100km south of Paris.
Hutchinson is still on the same site, with one of the original buildings, which has a roof designed by Gustav Eiffel, used as a training and media centre. Today, Hutchinson makes around 5000 tyres a day, not just in its own name but for other well-known bike brands. It also makes parts for automotive, railway and aerospace applications and employs over 40,000 people worldwide.
New rubber development
Hutchinson puts a lot of resources into research and development, with around 300 people working in its labs. There’s a pilot-size rubber mixing facility, which can make test batches of between 300g and 3kg for physical and chemical characterisation.
When it introduced its latest Fusion 5 tyre a couple of years ago, Hutchinson’s chemists felt that they could improve on the formulation of the compound used. The result was the company’s new 11Storm rubber, which is used in all its Fusion 5 tyres manufactured after May 2017.
A new compound undergoes a battery of tests of its physical characteristics and chemical composition before launch. The labs use advanced techniques including electron microscopy, nuclear magnetic resonance and X-ray tomography to understand the structure of a prototype rubber sample.
>>> What effect do tyres have on aerodynamics?
There’s also a large computing facility. For a new bicycle tyre, this is used to simulate the effect of turning and hitting obstacles on the prototype tyre’s casing.
Industrial production
The process of making a cycle tyre starts in the rubber mixing plant. This produces around 40 tonnes of rubber compound a day from two mixers. A batch may include around 30 different ingredients, including different grades of natural and synthetic rubber, plasticising agents, carbon black and sulphur.
The different components of a cycle tyre are manufactured in separate processes in other parts of the plant. The casing is made of woven nylon, with either 60 or 120 threads per inch. This is coated with rubber, using a machine which originally dates from 1910. Because a 120tpi casing requires less rubber to coat it than a 60tpi casing, it’s thinner and more subtle. Casings are cut to size on the diagonal from the rubber-coated sheet.
>>> Should you change to winter tyres?
The beads are also pre-coated with rubber before tyre assembly. Hutchinson uses steel wire, Kevlar or carbon fibre. Carbon fibre is used for the beads of tubeless-ready road tyres.
>>> Will carbon clincher wheels kill off tubular tyres?
Tyres are assembled from their components by hand on a rotating metal drum. First the casing is laid down, then the beads are added, guided by laser. Finally, the under-tread protection and the rubber for the tread are added and the ends of the tread heat sealed together, before the logos are added.
Then it’s time to vulcanise the tyre, to harden up the casing and seal the different components together. This process uses steam and pressure to heat the tyre to 269C for between 3 and 6 minutes. The metal dies used also add the tread to the tyre.
>>> The best road bike tyres reviewed
Completed tyres are checked twice for visual defects, before going off-site to be packaged. There’s a quality control lab alongside the factory floor, which tests tyres for rolling resistance, ozone stability, snakebite resistance, bead stretch and other properties. One machine tests resistance to bursting when the tyre is overinflated.
Thank you for reading 20 articles this month* Join now for unlimited access
Enjoy your first month for just £1 / $1 / €1
*Read 5 free articles per month without a subscription
Join now for unlimited access
Try first month for just £1 / $1 / €1
Get The Leadout Newsletter
The latest race content, interviews, features, reviews and expert buying guides, direct to your inbox!
Paul started writing for Cycling Weekly in 2015, covering cycling tech, new bikes and product testing. Since then, he’s reviewed hundreds of bikes and thousands of other pieces of cycling equipment for the magazine and the Cycling Weekly website.
He’s been cycling for a lot longer than that though and his travels by bike have taken him all around Europe and to California. He’s been riding gravel since before gravel bikes existed too, riding a cyclocross bike through the Chilterns and along the South Downs.
-
Trek, State and Specialized raise bike prices while other brands limit US releases — Is this just the beginning?
As tariffs hit, the bike industry is forced to adapt, whether through price increases, limited releases, or a restructuring of supply chains
By Anne-Marije Rook
-
How I got my non-cyclist friend hooked on riding bikes — and how you can, too
With a little bit of gentle guidance, “bikes aren’t my thing” can turn into “when’s our next ride?”
By Marley Blonsky