Inside Miche: how a 98-year-old company adapted to the 21st century
Miche still makes its products in its factory north of Venice. But robotics and computerisation give it the edge over the Far East
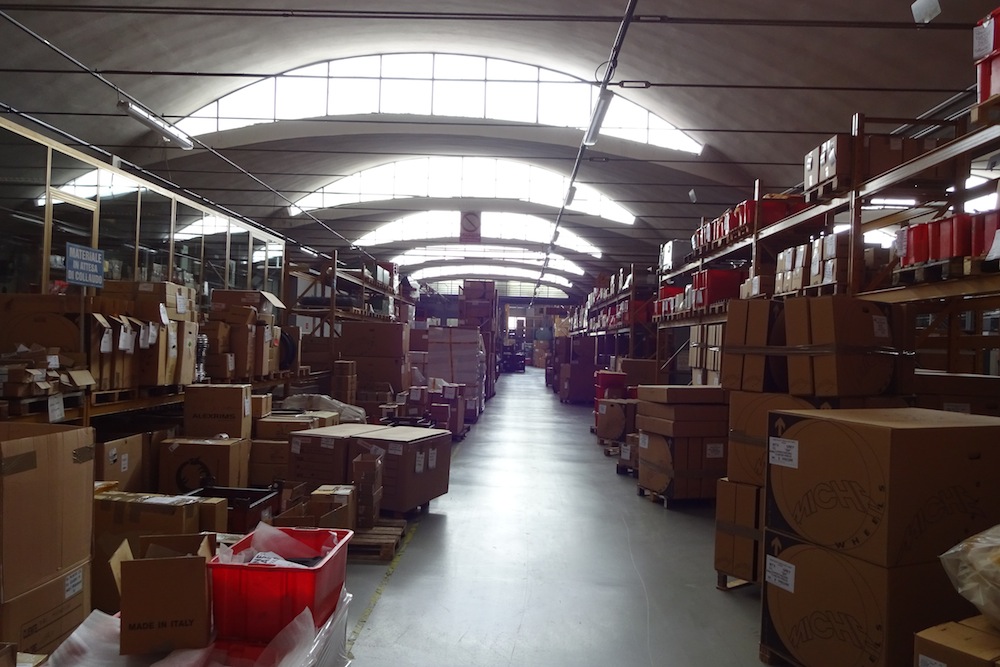

Miche makes a huge range of products – over 10,000, including chainsets, cassettes and wheels. It sells them under its own name but also makes equipment under contract for other well known brands and as OEM for bike manufacturers. Miche also makes custom products, like the freewheel bodies used in Elite’s turbo trainers.
Its two wheel lines, one for shallow wheels and another for its new deep section rims, make around 120 wheels an hour; that’s 60,000 a year. The wheels are laced by hand before a first machine pretensions the spokes.
A second machine trues the wheels automatically, taking around 100 seconds per wheel. Miche works to +/- 0.2mm, better than most wheelmakers’ +/-0.3mm.
Miche makes its own hubs too, assembling the higher quality ones by hand. It’s tested ceramic bearings, but says that their longevity is less than steel and they do not justify the extra cost. Miche offers a two year warranty on its hubs.
Miche puts a lot of resources into quality control too. Its carbon rims come in batches of 200. Of these, one rim is cut open to ensure that the interior carbon lay-up is correct, while another is made into a test wheel that is put through 450 acceleration and braking cycles, testing both hard braking from 44kph to zero and longer, softer braking action.
A probe measures the rim’s surface temperature, which can reach 150C. Braking performance is recorded by the machine, which can also simulate wet conditions.
Miche also makes around 10,000 cassette sprockets per year. They’re punched out of a continuous strip of steel as blanks then CNC machined. All its chainrings are CNCed from blocks of aluminium rather than being punched. The large chainring blanks are 4mm thick, while small ring blanks are 3mm thick. Some rings use 5mm thick blanks, while 15mm blanks are used for single rings.
The blanks are fed into the CNC machines by robots that also retrieve and stack the finished product.
All the waste from the CNC machines is collected for recycling.
Thank you for reading 20 articles this month* Join now for unlimited access
Enjoy your first month for just £1 / $1 / €1
*Read 5 free articles per month without a subscription
Join now for unlimited access
Try first month for just £1 / $1 / €1
Get The Leadout Newsletter
The latest race content, interviews, features, reviews and expert buying guides, direct to your inbox!
Paul started writing for Cycling Weekly in 2015, covering cycling tech, new bikes and product testing. Since then, he’s reviewed hundreds of bikes and thousands of other pieces of cycling equipment for the magazine and the Cycling Weekly website.
He’s been cycling for a lot longer than that though and his travels by bike have taken him all around Europe and to California. He’s been riding gravel since before gravel bikes existed too, riding a cyclocross bike through the Chilterns and along the South Downs.
-
'This is the marriage venue, no?': how one rider ran the whole gamut of hallucinations in a single race
Kabir Rachure's first RAAM was a crazy experience in more ways than one, he tells Cycling Weekly's Going Long podcast
By James Shrubsall
-
Full Tour of Britain Women route announced, taking place from North Yorkshire to Glasgow
British Cycling's Women's WorldTour four-stage race will take place in northern England and Scotland
By Tom Thewlis