Could frame facing solve creaky bottom brackets and rubbing disc brakes?
Mass production means that frames can be imperfect, and components can wear out quicker than you'd expect. So is a little extra TLC the answer?
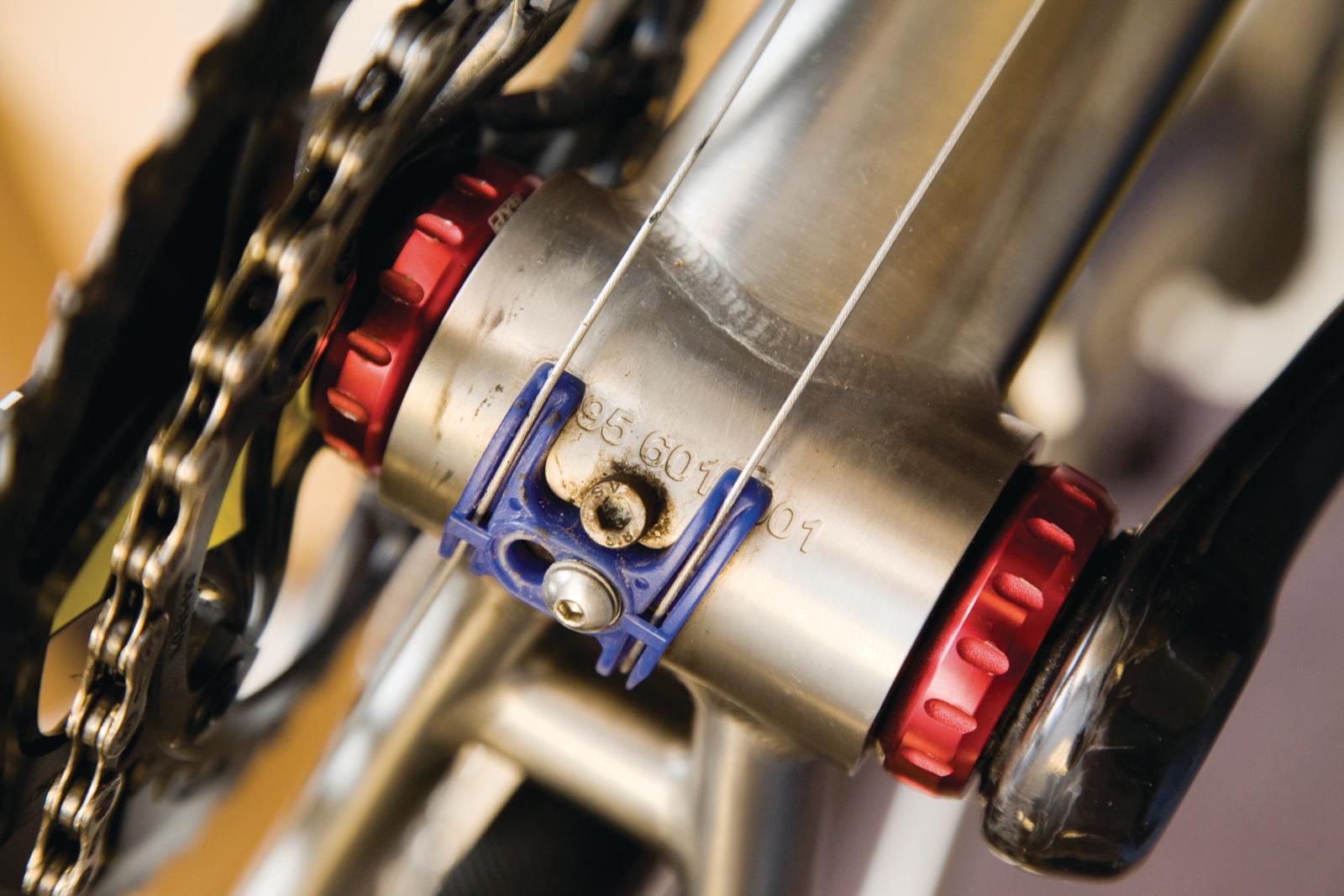
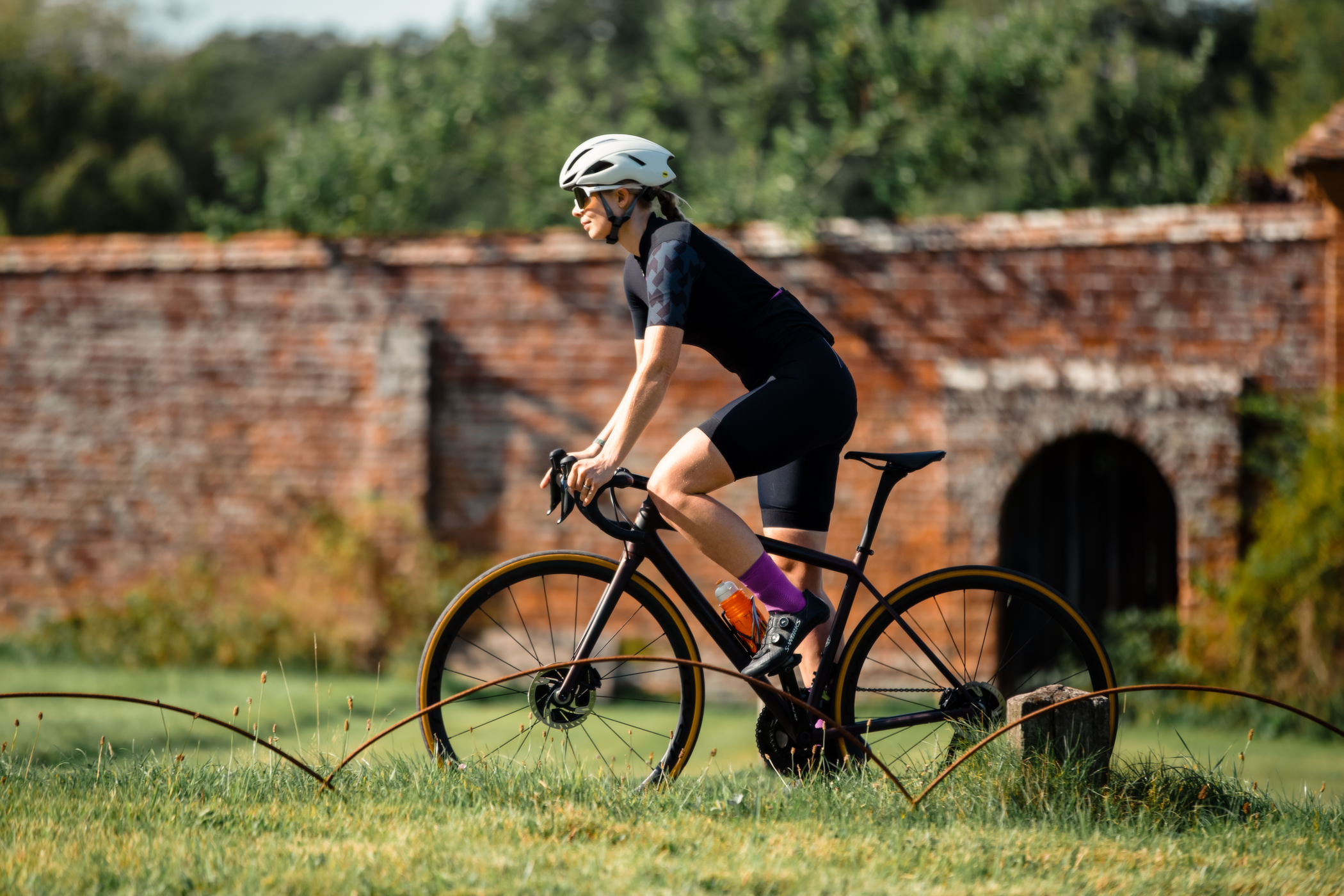
Creaky bottom brackets and rubbing disc brakes are extremely common complaints among amateur cyclists, as well as pros. Often, the temptation is to turn to the components themselves with ire and frustration, but in some instances, the fault may lie with the frame that the seemingly noisy parts are mated to.
That’s where facing can come in. Facing is often used as an umbrella term to refer to any job which involves removing excess material from a bike frame. Closely related is reaming – cleaning out or enlarging a hole – and tapping, which is the process of cleaning out a thread or re-cutting a new thread.
A mechanic will apply this process to any part of the frame or fork which needs to be mated to a component: head tubes, stems, disc brake mounts, bottom brackets.
You could have a go yourself, but it's a precision job - and a full set of tools could cost you "from £1000", to the "£6000 to £8000" that VeloAtelier's Lee Prescott - who designs and manufactures his own frames as well as building up those produced by other brands - tells us he's invested over the years.
What does facing involve and what problems can it solve?
Shaving off grams and saving seconds via aerodynamic optimisations are headline-grabbing, incremental improvements that the bike industry loves to celebrate. But there's certainly a sizeable congregation of consumers who would be more enamored with a bike that works efficiently year, after year, after blissfully silent year. And it's important to note, from the outset, that there are hundreds of thousands of cyclists out there enjoying exactly that - but understandably - discontentment tends to shout louder than satisfaction.
The sort of longevity that yields years of joyfully silent transmission is not found in a windtunnel or on the scales. It is achieved by having a frame where the interfaces are up to tolerance - meaning - built within a window of fit which allows the components to perform at their best.
Bottom bracket shells
A bottom bracket shell that is exactly the right size and shape will mean that the bottom bracket sits straight, and the crankset will run smoothly.
Facing a bottom bracket shell involves checking that, if it's threaded, the threads are clear, free and the hole is round. The faces on both sides should be parallel, straight and flat, "so that any cup that’s biting into it is pushing in level and maintaining a level of parallelism,” says Prescott, who designs and manufactures his own metal frames for Meteor Works, but also works with third-party carbon manufacturers, and services bikes from brands across the industry.
If this is not carried out, the symptoms will include creaks that “can’t be defined”, he says. There’s a performance element, too: “People chase every single watt, and spend loads of money on ceramic this and aero that – but having bottom bracket bearings that run concentrically and efficiently will probably save them way more lost power.”
Prescott faces the bottom bracket shells of all the metal bikes he builds for Meteor Works, quoting “about £100” for facing a frame as part of a service. Aeightbikes' mechanic Glen Whittington came in with a figure of £45 to £60, “to check everything – headset, bottom bracket, seat tube, tap out bottle cage bosses.”
But carbon is more complex, and more costly.
"Facing is much more prevalent on metal frames because on a metal frame you have to overcome any warping or distortion that's happened during the welding process. On a carbon frame, they come out of very expensive moulds, so provided all has gone well with the build - the layup is in the right place, the shrinkage has happened at the appropriate rate, the humidity is [as it should be] - it should mean that the frame comes out in a pretty good state.”
Not all carbon goes into the mould by hand, as per this meticulous process at the Hope factory. Image: Andy Jones
A lack of available tooling means that facing the bottom bracket shell of a carbon frame that’s slightly out of tolerance is time-consuming and probably not cost-effective, we were quoted one to two days' labour, or £400 to £800, to prepare an entire frame.
“You can normally get around these problems by the use of a good quality bottom bracket that's connected in some way, which will maintain the concentricity and parallelism of the bearings, reducing any issues you're going to get with misalignment,” Prescott says - pointing to a Wheels Industries produced design.
In normal circumstances, wearing at the bottom bracket that causes creaks will likely take time, “you may not see any issue within a couple of years,” Prescott notes, Aeightbikes’ Whittington, who works with teams as well as amateurs to keep their bikes in smooth running order, also suggested “about two years” as a reasonable time frame before the shell between your cranks may begin to groan.
The elephant in the room there is that many consumers buying mid-range carbon bikes will replace them within this time period. However, there are outliers. "If it’s wildly out, you’ll feel it straight away,” Prescott advises. “The crank won’t want to move freely, and if that’s the case you’re going to wear the bottom bracket out within months. If you ever come across that, actually that’s a manufacturing issue and a warranty issue, you shouldn’t be coming to a mechanic to get it sorted, you should be speaking to the manufacturer and having that resolved.”
The takeaway, then? For metal frames, checking the tolerances and facing if required seems an obvious investment to add to any build you intend to ride long term. If your bike is carbon, it's a job for those seeking the absolute ultimate in performance. For most of us, minor niggles can be addressed via component choice, major niggles via the manufacturer.
Disc brake bosses
Disc brake bosses are an area where facing can be extremely beneficial, and it’s an inexpensive procedure on both metal and carbon bikes. We've all heard riders - club mates, professionals, perhaps ourselves - lamenting the irritations of poorly set up disc brakes.
“The road standard system assumes everything is accurately made,” Prescott explained. “If the caliper mount is not perfectly perpendicular to the rotor, the pads are always going to be hitting the rotor at a slight angle. We're only talking fractions of a degree, but when the whole pad travel on a road disc is less than 1mm, fractions of a degree matter.”
Whittington agreed, adding: “A lot of people talk about the bedding in period [of disc brakes]. You do need to get a little bit of brake pad material on to the rotors, but that will happen really quickly. What’s often happening is that the pads aren’t hitting the rotor squarely, but after a few rides they’ll wear unevenly so that they are.
"Facing the calliper mounts would mean everything lines up straight away.”
Unlike the bottom bracket, where it might take time to notice an issue, in this area the symptoms can be immediate. “We can all hear a disc rubbing on rides straight away,” Prescott says, listing other symptoms as spongy braking and uneven wear to the pads.
This is a job you might even be able to do at home, a Park Tool DT-5.2 Disc Brake Mount Facing Set costs £465.
"The tooling exists for facing carbon disc brake mounts - so facing a carbon frame in that area is no more time consuming or expensive than doing a metal frame, and it's something most frames could benefit from, even if it's just to remove excess paint that's slightly misaligning the caliper," Prescott notes.
Headset
A quality headset, in a well toleranced frame, should last decades
Complaints around the headset are far less common, and perhaps that’s because they don’t make a noise. However, having a perfectly prepared frame can still pay dividends.
“With the headset we’re facing the surface that the bearing is going to mate to, cutting or abrading those faces so that they are parallel to each other and round, that way the bearings sit in alignment and prevent any excess wearing of the bearing,” Prescott outlines.
How do you know if the work needs doing? “If the bearings are misaligned, you’ll feel tight spots, so your steering won't be free and even.” After time, things can go the other way, “it can lead to the bearings pitting the races and you get ‘indexed’ steering.”
A “nice flat parallel bearing surface” ultimately allows components to last longer, “I have a Chris King headset that’s lasted over 20 years,” is Prescott’s example.
Should we even need to face frames?
Not every mechanic believes frames need to be faced. In the course of researching this article, I spoke to seven representatives, ranging from independent mechanics to shops. Four said it wasn’t necessary, and that modern frames are typically within good working tolerance, whilst three were in favour, lamenting stories of bad quality frames across a range of price points.
One bike shop owner commented: “You get the occasional frame that needs facing, but it’s very rare. It’s not something we’d do on a new frame as standard.”
The difference in opinion could come down to a multitude of factors, but it is fair to say that some frames come out of their factories in a better state than others.
Every bike manufacturer working will have a defined level of Quality Control (QC). This is made up of two factors: tolerance, the window if fit which is deemed acceptable, and consistency - how repeatable this is.
“With anything, the higher tolerance you want something, the more laborious that process becomes, hence the more expensive. Also, accurately measuring it becomes more difficult, hence it costs more,” Prescott says.
Brands will define how tight they want their tolerances to be, how many frames in every 100 or 1000 they want to be checked (taking care of consistency), and how stringent they want the reporting to be. Both Prescott, and the owner of a mass producing frame brand, gave 10-15% as the proportional increase on the RRP of a frame, when higher level QC is applied.
Adding £100-£150 to a £1000 road bike is a dealbreaker in the eyes of most consumers purchasing at that level, especially if they're unlikely to notice the byproducts of imperfections during the oft reported ownership span of under two years (how sustainable this is, is another question).
“If you’re trying to put out a £1000 complete carbon road bike, you’re not going to be able to physically afford the highest levels of quality control. It would make it not a commercially viable option. It means that all those people who now have £1000 road bikes, and are getting into the sport, wouldn't have had that opportunity," Prescott points out, adding confidently "there is a place for all levels of QC."
The level of QC, and attention to facing and finishing, varies per brand and per factory. Speaking to Canyon, representative Jack Noy told me: "Our frames are quality inspected and facing/finishing tooling forms a key part of our finishing process to ensure areas which rely on accurate tolerance for optimum performance - such as brake mounts, BB shells and headtubes - are to the highest standard."
The direct-only brand lacks the benefit of bricks and mortar stores, so builds take place in-house, not at a third-party local bike shop. Noy said this makes high-quality frame finishing a key focus, "as a brand who assembles thousands of our own complete bikes each year in-house, it is within our interest to ensure fitment and tolerances are to spec- to streamline the build process and offer our customers the best experience possible."
Should you have your frame faced before it’s built up?
There are thousands of cyclists riding around on unfaced frames, enjoying every pedal stroke, and their bikes may last for years.
The necessity of facing likely depends upon how much you value perfection, how long you’re going to keep the bike and, of course, the quality of the frame as standard.
If you’re buying a £500 aluminium bike, an extra £50-£100 on facing is a big percentage increase, especially as you're quite likely to trade the bike in before issues arise. If your bike is carbon, the cost of facing the entire frame could exceed £800 (we were quoted two days’ labour). So, again, it might not be worth it. If you’re going through bottom brackets in a matter of months, we suggest you take the issue up with the manufacturer. However, for a metal frame which you intend to keep for years, it seems like a worthwhile investment - and regardless of frame material, we’d always say ‘yes’ on the brake bosses.
This article was originally published in June 2020, and updated in March 2022 following further interviews; some of the opinions quoted date back to 2020 interviews.
Thank you for reading 20 articles this month* Join now for unlimited access
Enjoy your first month for just £1 / $1 / €1
*Read 5 free articles per month without a subscription
Join now for unlimited access
Try first month for just £1 / $1 / €1
Get The Leadout Newsletter
The latest race content, interviews, features, reviews and expert buying guides, direct to your inbox!
Michelle Arthurs-Brennan the Editor of Cycling Weekly website. An NCTJ qualified traditional journalist by trade, Michelle began her career working for local newspapers. She's worked within the cycling industry since 2012, and joined the Cycling Weekly team in 2017, having previously been Editor at Total Women's Cycling. Prior to welcoming her first daughter in 2022, Michelle raced on the road, track, and in time trials, and still rides as much as she can - albeit a fair proportion indoors, for now.
Michelle is on maternity leave from April 2025 until spring 2026.
-
'I'll take a top 10, that's alright in the end' - Fred Wright finishes best of British at Paris-Roubaix
Bahrain-Victorious rider came back from a mechanical on the Arenberg to place ninth
By Adam Becket Published
-
'This is the furthest ride I've actually ever done' - Matthew Brennan lights up Paris-Roubaix at 19 years old
The day's youngest rider reflects on 'killer' Monument debut
By Tom Davidson Published