There are not many things you can rely upon in this world, but my Hope hubs are a rare exception
Mechanic Glen Whittington had the Hope hubs recommended to him over 20 years ago, and they're still going strong
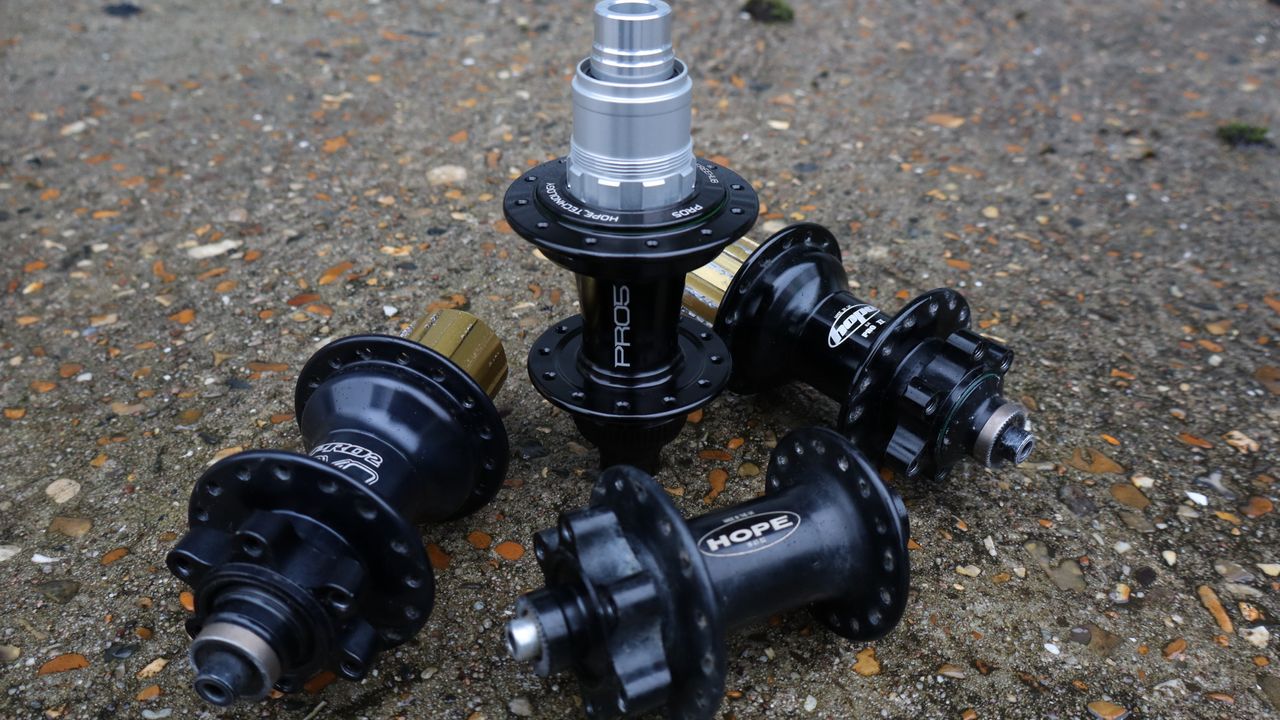
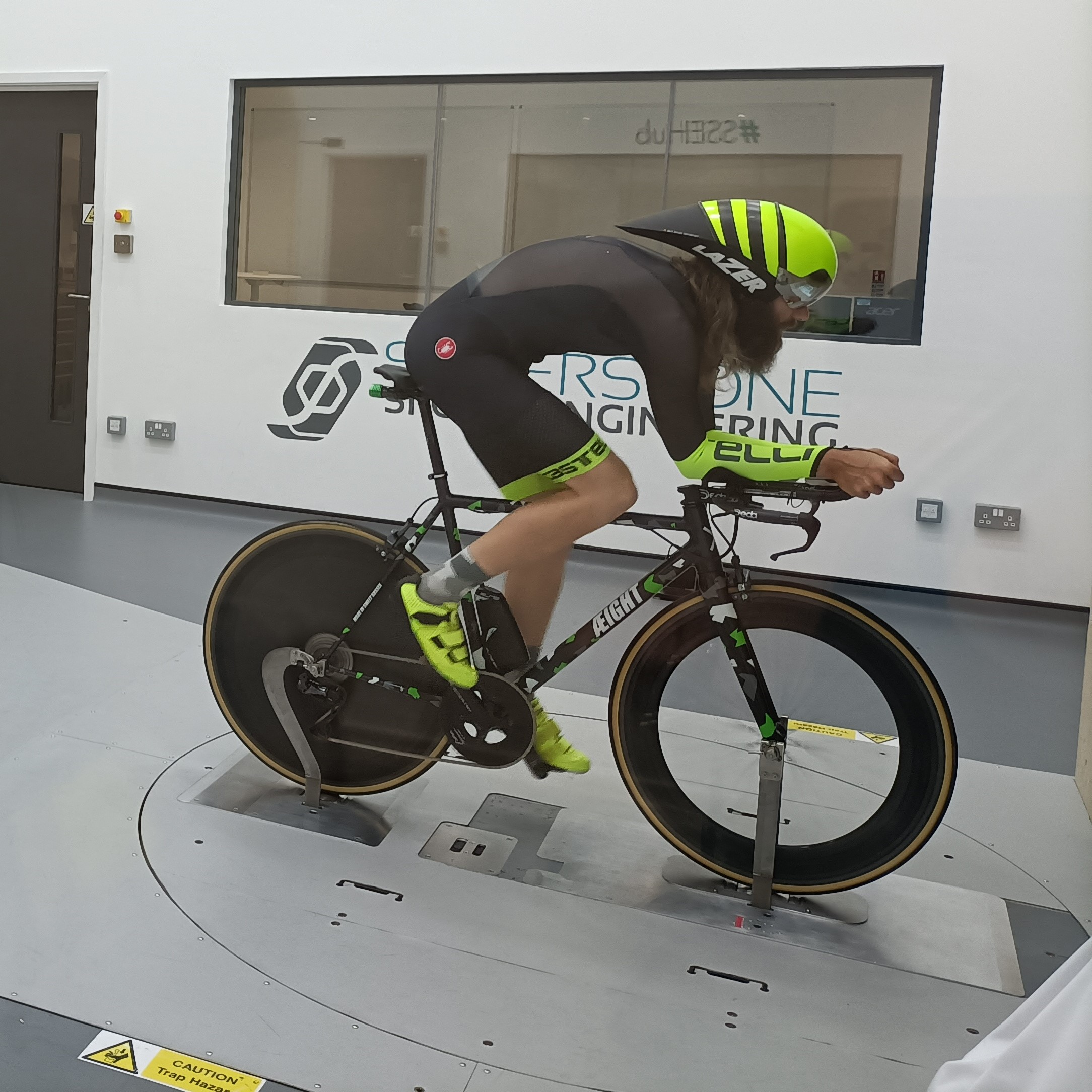
This article is part of a series called ‘A love letter to…’, where Cycling Weekly writers pour praise on their favourite cycling items and share the personal connection they have with them.
The below content is unfiltered, authentic and has not been paid for. Today's love letter comes from Cycling Weekly contributor, and full-time mechanic, Glen Whittington.
There are few things in this life that you can depend upon, and bike parts are not usually one of them - we accept that lightweight parts are likely to wear out at some point. But, over 20 years ago I was told to buy a set of Hope Hubs because, “they’re indestructible”, my friend advised, “I’ve ridden these through two winters and never even touched the bearings”. As it turns out, he was right.
An increasing appetite for information among customers means that the technical aspects of almost components are made transparent from purchase, but wheelbuilding has kept much of its mystery, superstition, and art over the years, and it’s one of the few jobs which most mechanics still struggle to master. It takes a mix of time, patience, and skill to perfect, and the humble hub sits at the centre of the process, almost like the beating heart of the wheels. There’s something very “alive” about a quality hub.
It’s the first tactile thing that you pick up when you’re building a pair of wheels and the Hope rear hubs have always sat nicely in my grasp as I take the vital measurements needed to calculate spoke length with. In fact, I find it absolutely impossible to avoid clicking the freehub as I go, like some kind of deluxe fidget spinner.
Where I feel unconnected to most components, which seem to have been made by a machine in a far away land, there's something special about the Hope hubs - you can see the various manufacturing processes if you look closely and admire the workmanship. The hub starts life as a blank, vaguely hub shaped aluminium billet. This is then milled by a machine which changes tools as it works for various processes, inside and outside of the hub.
The hub shell is then polished and checked both by eye and with a range of gauges to ensure that everything is perfect, before it’s anodised in one of the famous colours. Graphics are then laser etched to complete the process. All of the hub components, with the exception of the bearings, are made in-house by similar machines, programmed and controlled by the locally based workers. Those components are then hand assembled to suit the order book, one at a time, before being packed and dispatched to someone like me.
Get The Leadout Newsletter
The latest race content, interviews, features, reviews and expert buying guides, direct to your inbox!
Once I’ve built the hub into a pristine set of wheels, it’s time to go and get them filthy. There’s nothing that doesn’t get thrown at these hubs - water and mud from the road, mud and grit off-road, and all manner of unmentionables from other road and trail users. I’ve raced my wheels on sandy cyclocross courses, fitted them to heavily laden touring bikes, and taken them mountain biking all over the world.
Over the years I’ve added to my armoury. I started with the “XC” model, and briefly had a set of “Bulbs”. I have a set of the “Pro2” hubs built up. I skipped forward to the “Pro4” when it came out and built over 100 sets of these for customers - most of which I rarely see thanks to the build quality and the excellent seals. I currently own several sets myself, and then last year, along came the updated “Pro5” which I had to have. Despite my growing collection, after 20 years, my original set of XCs are still built up, in use and going strong. I’m fairly certain they’re on only their second set of bearings and I had to rebuild them in about 2006 with new rims due to pilot error, but the hubs appear to be indestructible.
Of course, technology is constantly evolving. Hope has not stood still, so there have been some tweaks made along the way, but essentially everything that you get on the new hubs is an evolution of the design rather than a design change. It’s pretty impressive to me that the designers at this relatively small UK firm were so far ahead of their time, that a 23 year old hub is not just still rideable, despite some concerted effort from myself. . And even more remarkable, if I were to break something, they still keep and manufacture spare parts for much of their back catalogue.
In my experience there’s not many things you can rely upon in this world, but my Hope hubs are a rare exception.
Thank you for reading 20 articles this month* Join now for unlimited access
Enjoy your first month for just £1 / $1 / €1
*Read 5 free articles per month without a subscription
Join now for unlimited access
Try first month for just £1 / $1 / €1
Glen’s an ex-racer who still finds time to ride bikes for SDWRacing. He started racing in 1998, initially specialising in XCO and Solo 24-Hour Mountain Bike. He became a mechanic in 2002, working in shops and also for professional race teams. During this time he spent more time racing cyclocross and road, and then also time trials. In 2013 he built his first bespoke frame and then spent several years at Roberts learning the art. Since then he’s designed, tested and now sells frames/bikes to the public as part of his ÆIGHT brand.
-
How to watch Gent-Wevelgem 2025: Everything you need to live stream the Flemish Classic
All the information on broadcasters and live streams for Gent-Wevelgem on 30 March, as the Spring Classics continue in Flanders.
By Adam Becket Published
-
Is creatine a useful supplement for cyclists?
One the few supplements with a strong evidence base, creatine promises explosive gains, finds Rob Kemp
By Rob Kemp Published