Are carbon rims really stronger than aluminium ones?
How is carbon-fibre, with its reputation for being lightweight but prone to catastrophic failure, now being ridden routinely by mountain bikers?
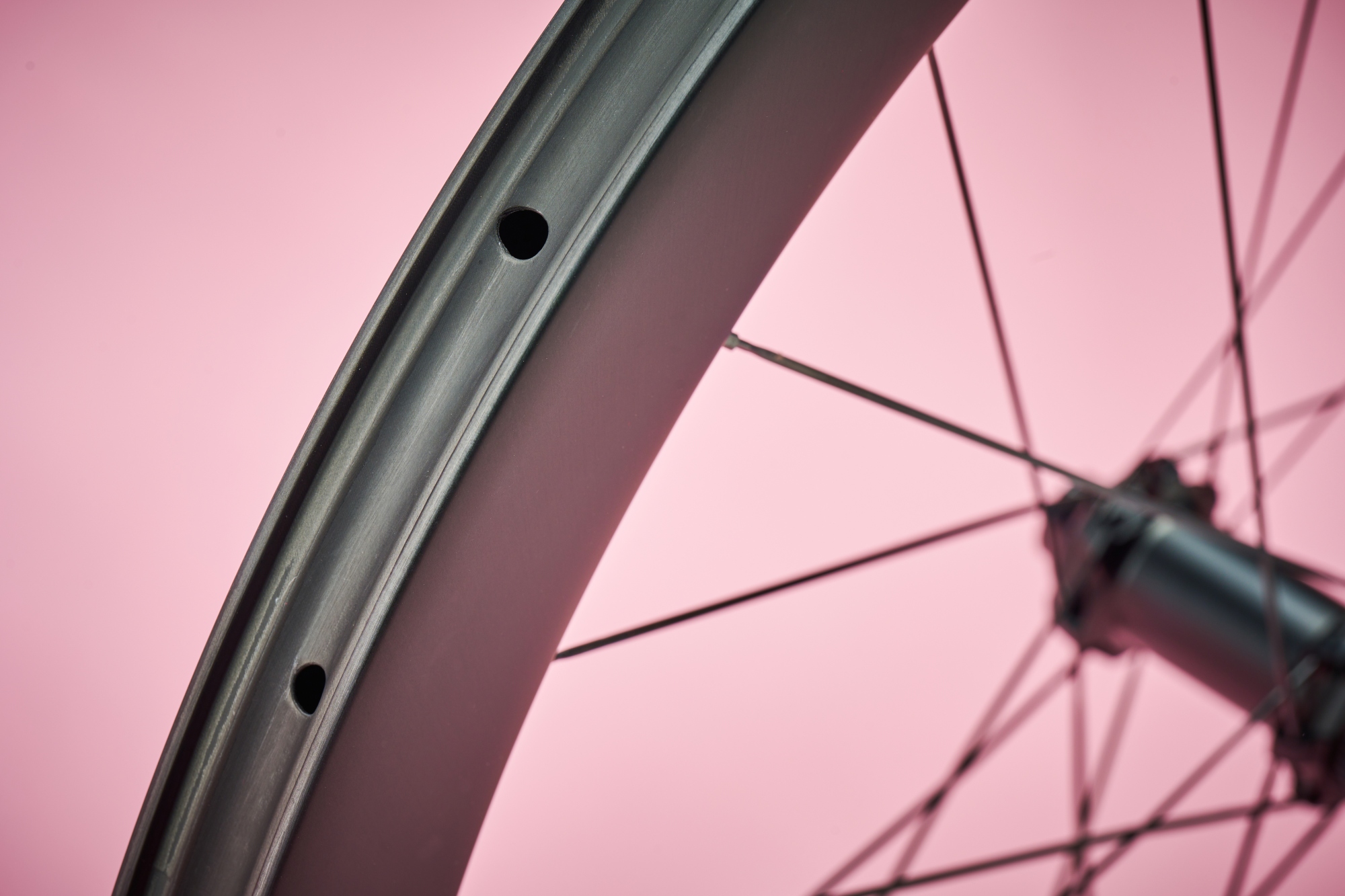
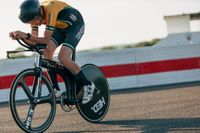
In 2010 Fabian Cancellara won Paris-Roubaix for the second time. He attacked at Mons-en-Pévèle and soloed to the velodrome two minutes ahead of Thor Hushovd.
It might have been just another incredible performance in a spectacular season: the Swiss rider had already won Milan-San Remo and the Tour of Flanders, and would go on to win the Tour de France prologue and the World Championship time trial. But there was something different about this victory: it was the first time the ‘Hell of the North’ had been won on carbon wheels – Zipp 303s.
Cancellara en route to winning the 2010 Paris-Roubaix
At the time it was seen as a huge technological turning point, but carbon road bike wheels were still eyed with suspicion by the average rider. It might be fine for Cancellara who never goes anywhere without a following car packed with spare bikes and wheels, but could it really be trusted for everyday riding?
Thirteen years on the question has been answered many times over. Carbon is not only capable of withstanding the toughest terrains but wheel brands’ impact testing is now showing that carbon rims are actually stronger than their alloy counterparts.
One of these brands is West Sussex-based Hunt Wheels, which most recently has been testing its Proven Carbon Race Enduro mountain bike rims against its aluminium Enduro Wide mtb rims – and other competitor rims – on its custom impact rig, which drops an anvil directly onto the rim, with the weight and shape of the anvil and height of the vertical drop variable.
A graphic on Hunt’s website has the carbon wheels taking significantly more impact energy before they fail.
"Absolute failure energy is higher on carbon"
Hunt engineer Paddy Brown
“The Proven Carbon Race Enduros fail at 160 joules where the rim is clearly broken, whereas with the [alloy] Enduro Wides we’re seeing damage at 120, sometimes 140 and then always failure by 160,” says Hunt engineer Paddy Brown, “so the absolute failure energy is higher on the carbon by a little bit.
The latest race content, interviews, features, reviews and expert buying guides, direct to your inbox!
“An aluminium rim can accumulate damage with repeated lower energy impacts. If you see five or six 120-joule dings around your rim, eventually that product is a write-off,” he says.
However, Brown does concede that with lower energy impacts on a carbon rim “there might be some microstructure damage that could weaken it over time that you wouldn’t know about. It’s a difficult one with carbon because without cutting it up and scanning it you don’t know.
“In riding situations it’s much more complex than just impact strikes,” Brown adds. “If you smack it hard on a rock you might have weakened the microstructure, which would lead to a failure further down the road and there’s a bit more complexity there. Whereas with an aluminium rim it dings and you can see the ding.”
However, Brown says, 160 joules is equivalent to a huge impact that most wheels will never be subjected to, simulated on the test rig by dropping a 25kg wedge-shaped anvil from a height of around 1.3 metres. “And obviously you’re never hitting things square on - it’s always an angled impact – and mountain bikes generally have suspension.”
If carbon does crack without catastrophically failing, which is how Hunt intends it to happen, Brown explains that the crack will nearly always propagate from the rim hook down because that’s where the peak force is, so it’s generally possible to see damage.
What about road wheels ?
The UCI’s wheel test – for both carbon and alloy rims – requires a wheel to withstand a 40-joule impact from a flat steel anvil covered with a 20mm silicone pad to simulate a tyre. There must be no visible cracks or delamination and no change in lateral or radial profile in excess of 1.0mm.
Brown says Hunt’s road and gravel wheels are all tested at 40 joules – which is “like riding head-on into a kerb” – and expected to pass with no damage. Then they’re impacted at 70 joules, and he says Hunt uses slightly higher impact failures for gravel wheels.
“We make sure they can take a really big hit, and that if they take a really, really big hit the tyre will be retained and the rim will hold its structure – and that’s what we use the rig for most on the road side.”
Brown doesn’t claim Hunt’s road wheels are any more impact resistant than those of competitors and based on competitor testing puts the strength of Hunt’s wheels on a par with the Roval Rapide II – redeveloped after Peter Sagan destroyed a set of the original version.
“Their wheel performed well when we tested it,” says Brown. “It’s gratifying to see that they’re on a similar track.”
And finally, has there been some sort of new development or process since Cancellara’s win that has boosted the strength of carbon rims?
“It’s not something new that we’re doing,” says Brown. “We’ve had an impact test procedure since 2019 and we’ve just been increasing the amount of data we have, impact testing competitor wheels and working with manufacturing partners on evolving the shapes of our rims.
“The Proven Race Enduro is a new shape, with a geometry that is trying to dissipate the energy more effectively through the structure, but no, there is no magic bullet that has suddenly made carbon better. There is always that brittleness and fracture failure that’s hard to get around.”
Carbon v Aluminium according to Mavic
We asked Mavic – producer of the legendary aluminium Ksyrium wheels and at the same time famous for the classic Cosmic Carbones, one of the prettiest of the early carbon deep-section wheelsets (though admittedly a carbon fairing on aluminium rims) – to talk us through the pros and cons of carbon-fibre and aluminium.
“The characteristics of each material are very different,” says the French brand’s global PR manager, Michel Lethenet. “A material’s stiffness is measured in Young’s Modulus, which tells you the stiffness per unit of volume/mass in pascals or gigapascals. Based on that, a piece of carbon is stiffer per unit of mass than a piece of aluminium, titanium or steel. But carbon fibres need to work in the right direction to be stiffer than the other materials.”
Lethenet points out that aluminium alloy’s fatigue resistance is lower than that of carbon but it absorbs energy and deflects in case of shock, which is better for safety with the wheel going out of true but not breaking, meaning aluminium would deform under shock while carbon would crack.
Further, says Lethenet, “Aluminium dissipates and better resists heat when there is a high level of friction applied in the case of rim brakes. It supports tension whatever the tension direction [isotropic]; it is easier to machine and it’s cheaper to manufacture.”
As for carbon-fibre, Lethenet explains, “Its fatigue resistance is high, but the breaking point is instantaneous when the limit is reached as it’s not absorbing energy or deflecting under shock. Additionally, carbon concentrates heat at its defective point when there is a high level of friction applied [i.e. in rim braking].
“Carbon is strong if its fibres are uncut and aligned in the same direction of tension but otherwise has no strength at all; it needs to be properly woven or/and precisely laid up to resist tension and cannot be bent over a certain angle to keep its resistance characteristics (90° is not possible).”
Finally, Lethenet explains that carbon-fibre is expensive and delicate to manufacture, harder to build perfectly and manufacturers often need to overbuild the structure to compensate. For example, a 2-1.8mm-gauge butted stainless steel spoke is stronger (250daN yield stress) than a similar carbon spoke. A carbon spoke would need to be overbuilt to resist (going up to almost 500daN of resistance) and will resist only half of this (250daN yield stress) in case of hydrolysis. Lethenet explains that carbon-fibre has a higher sensitivity to hydrolysis than aluminium: the epoxy resin matrix resistance is halved after hydrolysis.
“To conclude,” says Lethenet, “both materials have benefits. For pure performance-oriented products, carbon keeps leading the comparison, but for most classic use cases, aluminium still has very interesting characteristics.”
We say...
The age-old belief that carbon will fail suddenly and catastrophically whereas aluminium will fail more slowly and predictably still seems valid due to the properties of the material. But if carbon rims are impact tested to a higher level than most will ever experience, it seems safe to trust the results of the impact test rigs. The fact that aluminium damage is in most cases more visible is a big plus point for it but, as Mavic says, it’s carbon that’s the leading material for performance- orientated products and that doesn’t look set to change any time soon.
The first version of this article was published in the print edition of Cycling Weekly. Subscribe online and get the magazine delivered direct to your door every week.
Thank you for reading 20 articles this month* Join now for unlimited access
Enjoy your first month for just £1 / $1 / €1
*Read 5 free articles per month without a subscription
Join now for unlimited access
Try first month for just £1 / $1 / €1
Simon Smythe is a hugely experienced cycling tech writer, who has been writing for Cycling Weekly since 2003. Until recently he was our senior tech writer. In his cycling career Simon has mostly focused on time trialling with a national medal, a few open wins and his club's 30-mile record in his palmares. These days he spends most of his time testing road bikes, or on a tandem doing the school run with his younger son.