Cranks that whiz at high speed are not a desirable feature, they’re just an invitation for crud to get into the bearings
CW’s Undercover Mechanic turns his attention to the murky world of bottom bracket ‘optimisations’
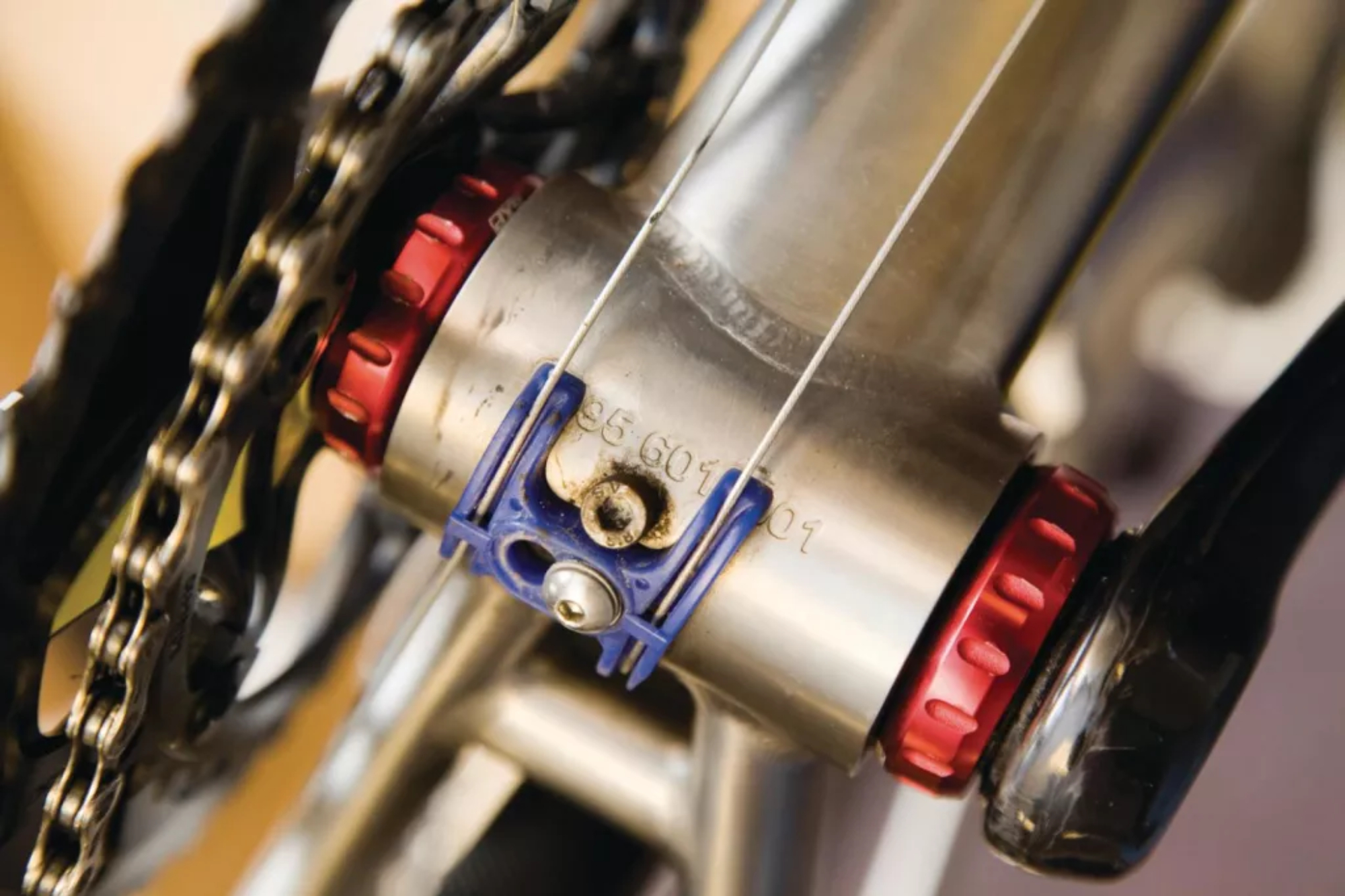
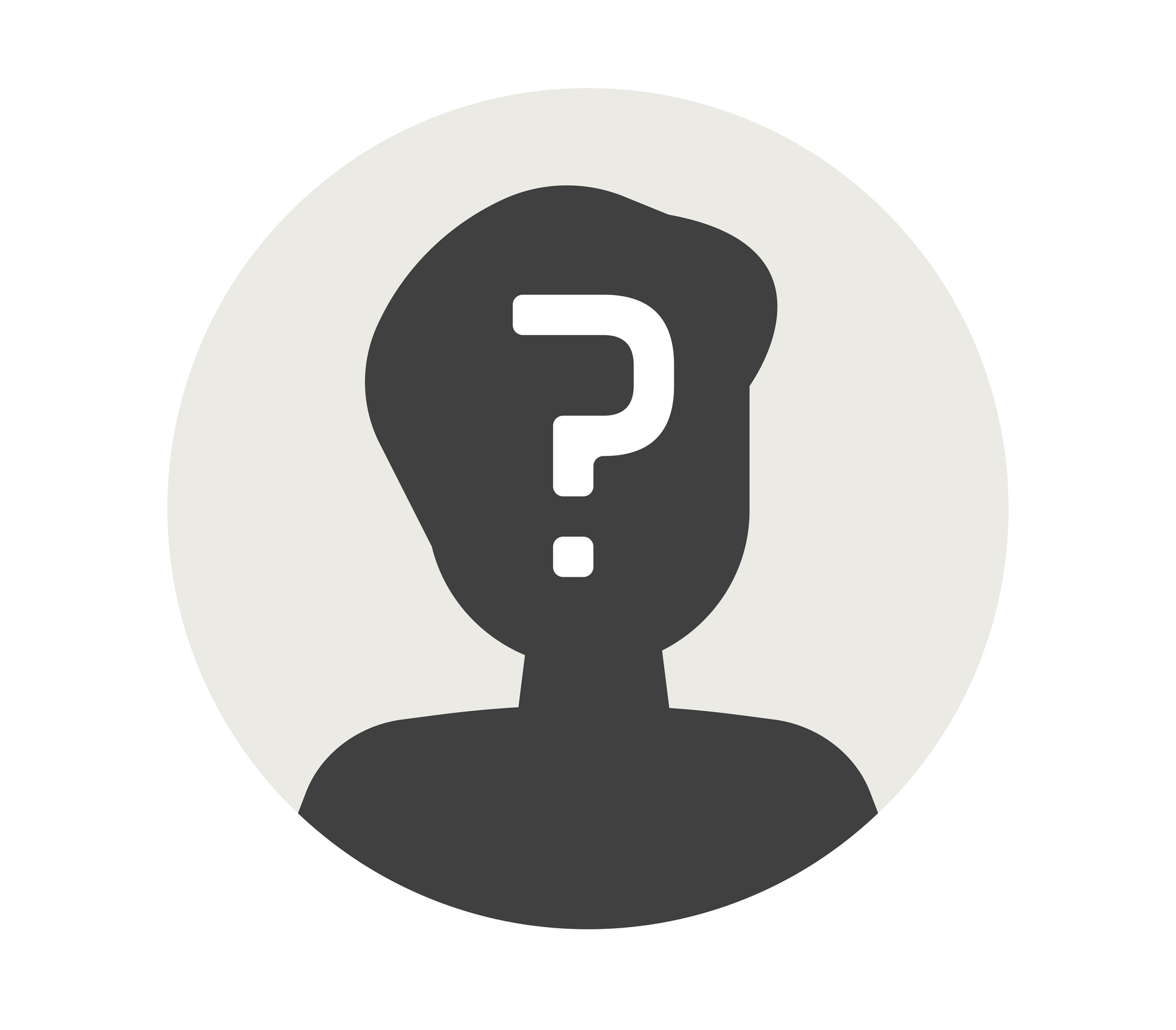
I was recently servicing an old vintage mountain bike from the 90s and was struck by how smooth the bottom bracket bearings were after almost 40 years. With modern bottom brackets, I would count myself very lucky to find bearings performing so well after even 40 months.
How have we got here? And why does it seem impossible for manufacturers to get bottom brackets right these days? I think to understand where it has gone wrong, we need to look at the evolution of the bottom bracket.
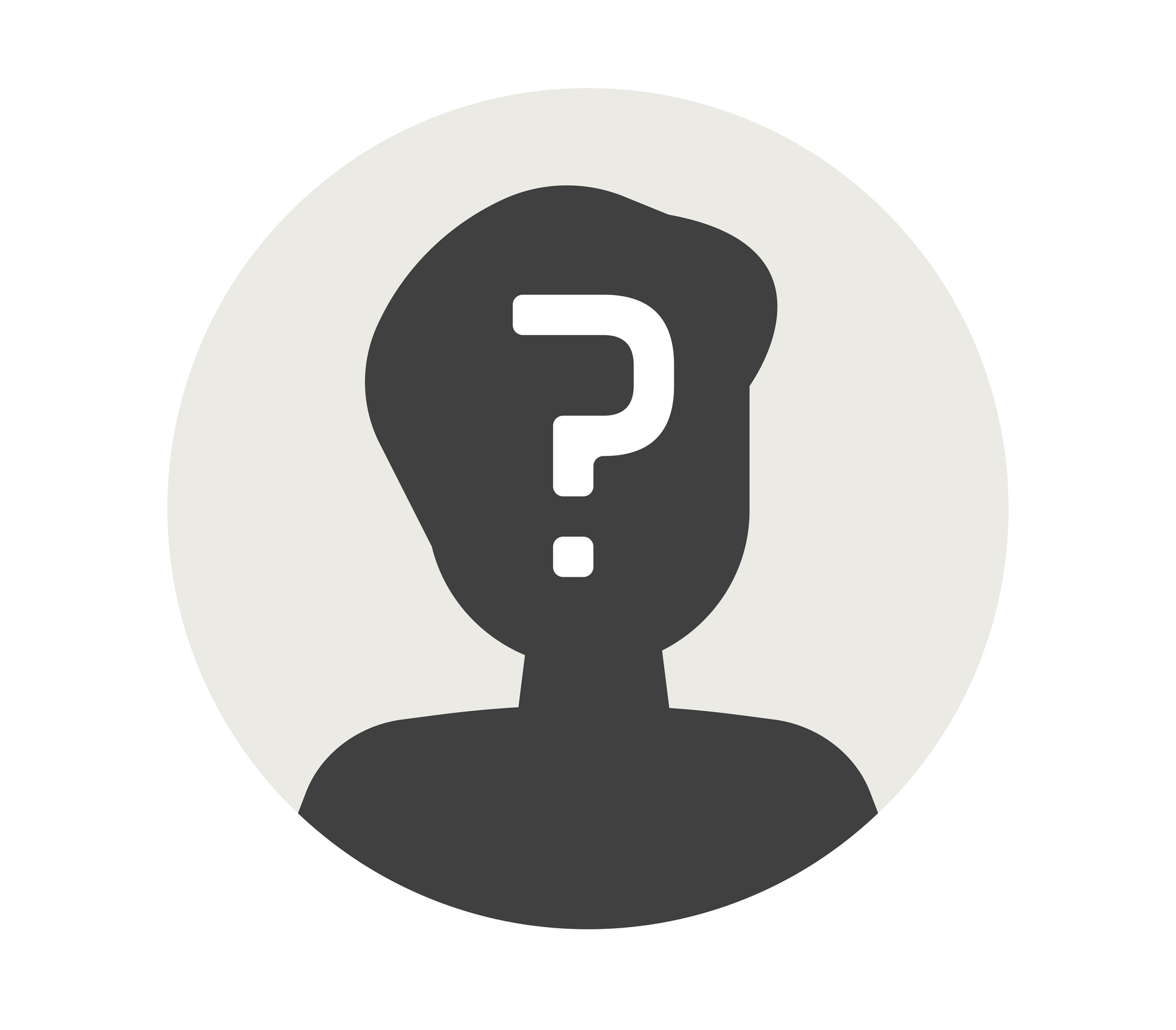
Cycling Weekly's Undercover Mechanic will be publishing his thoughts on the state of the industry once a month. He's been working with bikes for over two decades, offering servicing on models from some of cycling's best (and worst) marques. You'll find him at all major trade shows and events, just don't expect him to make himself known.
The original ‘modern bicycles’ used cup and cone bottom brackets [for an overview of all styles, check out this guide to bottom bracket standards]. In this system, the axle had ball races manufactured into it, these would guide the bearings, and then the cups that threaded into the frame would be adjusted to remove side-to-side play.
These gradually evolved into what we used to call cartridge bottom brackets. These all-in-one units had the bearings already fitted to the axle and preloaded, so all you needed to do was screw the whole unit in from one side and the opposite cup then just provided radial support. These inexpensive units would set a consumer back as little as £15, and the bearings would often last longer than the rest of the groupset. The key thing here is that the bearings and axle were both made by the same manufacturer, and, the bearing was preloaded and supported from both sides. The system could operate at its optimum, regardless of frame quality.
I’m not in the habit of harking back to the ‘good old days’, without acknowledging the pitfalls. Square taper axles did - if over-tightened - have an annoying tendency to flare the crank arm taper making the fit loose and therefore creaky. I remember on multiple occasions having to add small strips of ‘shim stock’ (read, Coke can, in non-mechanic speak) to the taper to try and eke out the life of a mistreated crank. Still, the systems, on the whole, worked well.
Then, the battle for lower overall system weights came to bottom brackets. The cycling industry moved to two-piece cranks, where the axle was now part of the crank and not the bottom bracket; it was all downhill from there, in my book.
The issue two-piece cranks created is that there is now the opportunity for this whole entity to consist of parts made by various different manufacturers, all with their own tolerances, eg, permitted variations from the specification.
Get The Leadout Newsletter
The latest race content, interviews, features, reviews and expert buying guides, direct to your inbox!
Creaks - which modern bottom brackets are renowned for - occur when there is unwanted movement between two parts, and, this is almost inevitable when tolerances do not align. Add to that the potential for misalignment that we now have by separating the two main bearings into unconnected separate cups, and, you’ve got a recipe for trouble. Even with a perfectly faced and reamed bottom bracket shell - whereby material has been removed to heighten the chance of a perfect fit - it only takes a fraction of a degree of difference in alignment to start creating problems.
Press-fit systems - the ‘go to’ of the 2010s, whereby the cups are pressed into the frame, with no cup - seem to take the brunt of the flack, with much of the industry now hightailing it back to threaded options. But actually, if you think about it, all bearings are press-fit, some are just pushed into a threaded housing first.
Press-fit bottom brackets, such as this BB386 EVO variant, enjoy a mixed reputation but it's often the quality of the frame that's to blame
There is nothing fundamentally wrong with a press-fit bottom bracket system if what you’re pressing it into is a perfect hole in the frame, and there’s the problem. One of the reasons that threaded bottom brackets have a slightly better reputation is because often it’s a single tube that is threaded which practically ensures a better concentricity in the bearings. Now that a lot of manufacturers are moving back to threaded shells in their carbon frames, where each side is not connected, I really hope they’ve spent the money making the moulds which are used to create the frames accurately, otherwise, we’re no better off.
Not only did the old one-piece cartridge bottom brackets of old ensure a well toleranced placement of the bearings, to prevent misalignment, but they also rarely needed re-greasing. This is because they tended to come with full contact seals in each bearing. Some of the really nice ones made by companies like SKF - one of the largest manufacturers of bearings - would also pack them with marine grease. Full contact seals and thick grease prevent the ingress of water and muck, so the bearing can run smoothly.
Unfortunately, the bike industry in its ultimate wisdom decided that this wasn’t good enough, as it increased drivetrain resistance, and thus had a negative impact upon the marginal gains sought by the uppermost echelons of our sport. In response, thinner greases and non-contact seals started to appear, all in the name of seeking performance over longevity and reliability. It still makes me shudder when I see a home mechanic spin the cranks in a ‘Dream Build’ video, cranks that whiz at high speed are not a desirable feature, they’re just an invitation for crud to get into the bearings.
What’s the solution? I’m certainly not advocating that we move back to square taper axles, however, having a bottom bracket unit where both bearings are pre-fitted into a toleranced shell makes a lot of sense, ensuring the bearings are concentric and parallel, and there are a few examples of these on the market now. One of the products I found interesting at the 2024 Eurobike tradeshow was the new bottom bracket unit from a small company called Bikone, a sponsor of the UCI WorldTour team, UAE Team Emirates.
The Bikone system mounts both bearings into a single housing, but also provides an internal preload by having a highly toleranced tube between both bearing inner races. This prevents excessive side-to-side loading, which ensures the bearings run beautifully smoothly and shouldn’t wear out anywhere nearly as quickly as the alternative. At the bargain price of almost £400, this new innovation arguably shares characteristics with the SKF-Thun cartridge BBs and Profile Racings BMX cranks from the 80s. I guess that’s progress.
Thank you for reading 20 articles this month* Join now for unlimited access
Enjoy your first month for just £1 / $1 / €1
*Read 5 free articles per month without a subscription
Join now for unlimited access
Try first month for just £1 / $1 / €1
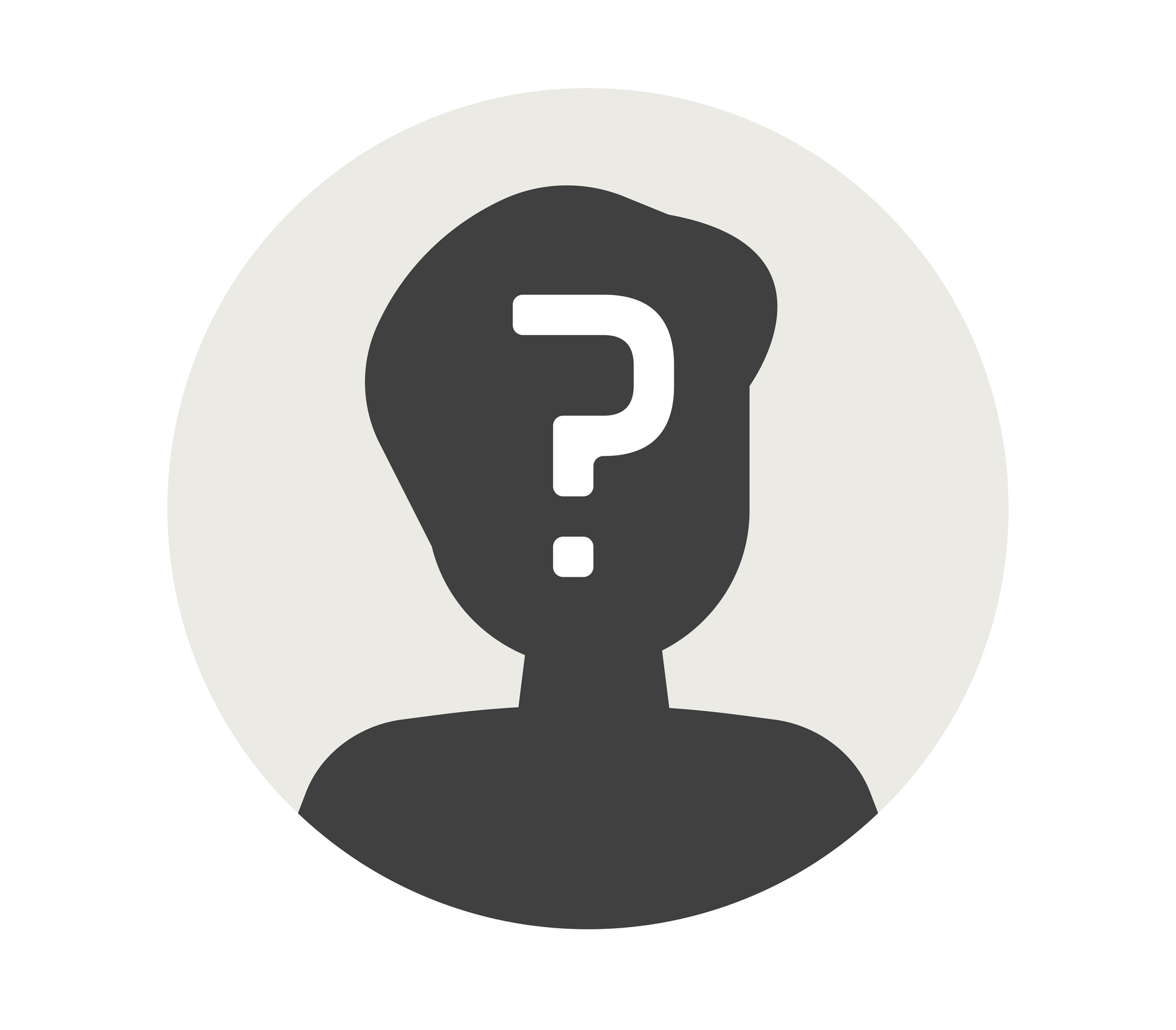
Cycling Weekly's Undercover Mechanic will be publishing his thoughts on the state of the industry once a month. He's been working with bikes for over two decades, offering servicing on models from some of cycling's best (and worst) marques. You'll find him at all major trade shows and events, just don't expect him to make himself known.
-
Trek, State and Specialized raise bike prices while other brands limit US releases — Is this just the beginning?
As tariffs hit, the bike industry is forced to adapt, whether through price increases, limited releases, or a restructuring of supply chains
By Anne-Marije Rook
-
How I got my non-cyclist friend hooked on riding bikes — and how you can, too
With a little bit of gentle guidance, “bikes aren’t my thing” can turn into “when’s our next ride?”
By Marley Blonsky