Six biggest irritants of modern bicycle design
Which areas of bicycle design could do with... a little bit of tidying up?
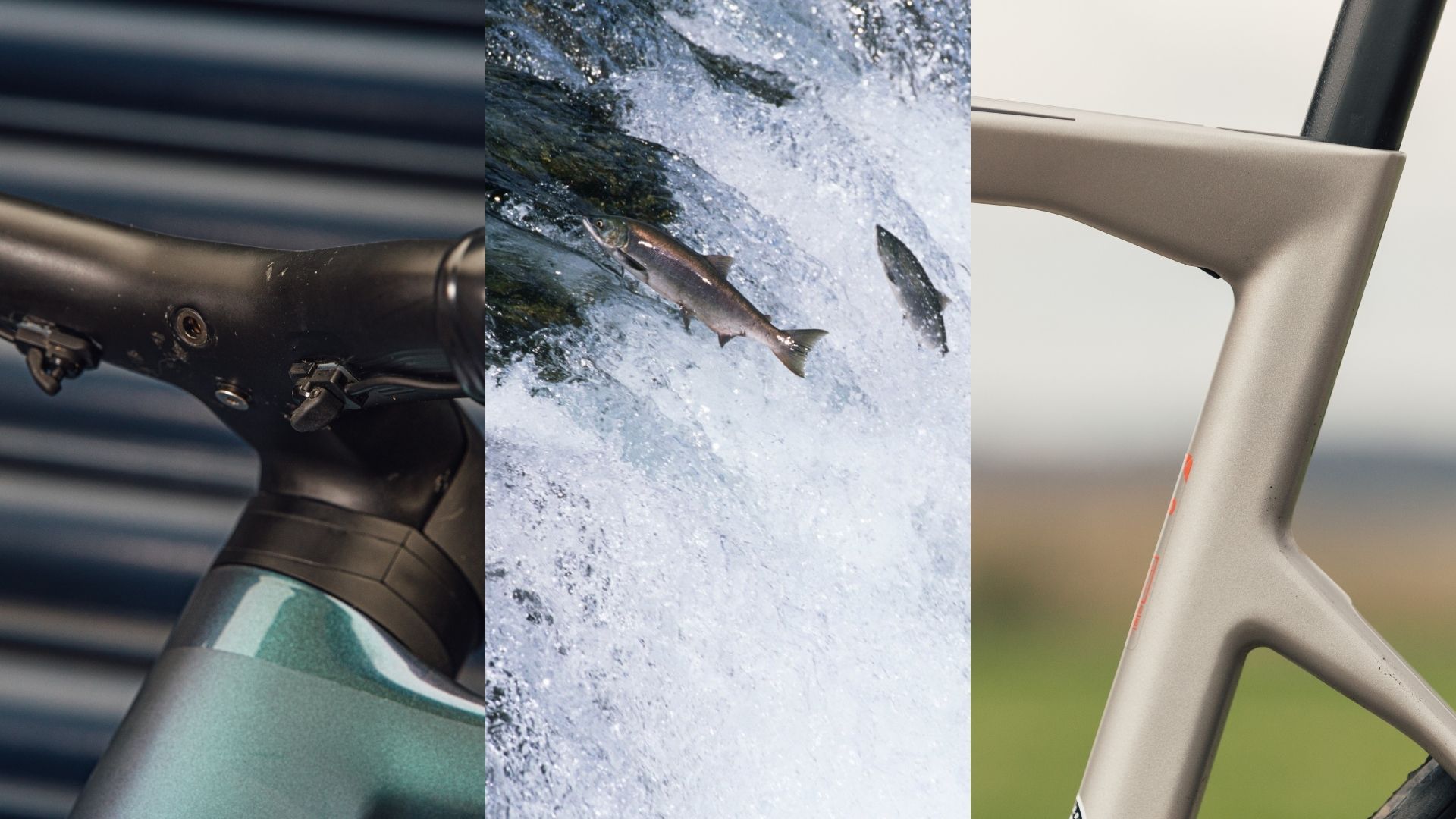
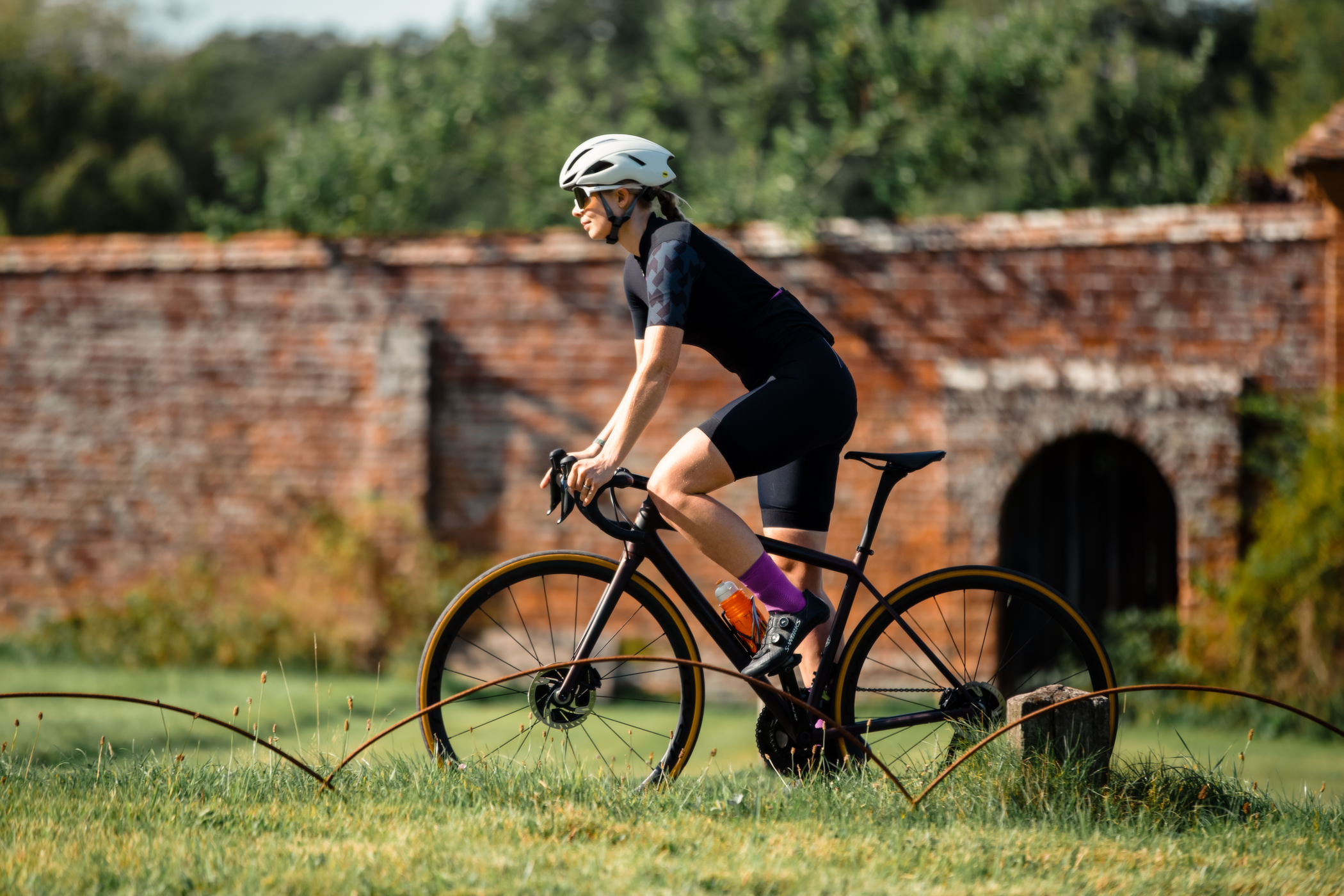
Trying to prevent technological advancement in any industry is a bit like swimming against a tide of schooling salmon. The UCI sticks its oar in sometimes, but good engineering always finds a way around.
If we didn't allow technology to advance, we’d all be riding around on the boneshaker bikes of 1869 - and we’d probably think the rattling experience was as good as it gets.
However, some advancements take time to reach refinement. Case in point, the first SRM power meter launched in the 1980s required a yellow pages sized instruction manual to just get going (or, so I'm told), early power meter pedals worked best if you sang a lullaby at the ideal pitch whilst tightening to optimum torque. But now? Anyone can fit a pair of power pedals to any bike and have accurate readings in seconds - albeit still at significant outlay.
Other advancements go full circle: Cannondale’s HeadShok of 1992 featured on early mountain bikes, it was fazed out when ‘real’ suspension arrived - but that elastomer/mechanical damper combo offering 50mm of travel looks real similar to some of the solutions we’re now seeing on gravel bikes. No prizes for guessing what’s next - lightweight air sprung forks, anyone?
En route to refinement, some advancements pose greater headaches for mechanics, engineers, bike testers like myself, and consumers. So - which “progressive” technologies do we all, quite frankly, want to either get in the sea (with the salmon) - or - hurry up and improve ASAP?
Proprietary seat posts
Propriatry seat posts can help brands save watts, add compliance and reduce weight - but they also tie you in
In the past, a bicycle brand would develop a frame, furnish it with a 27.2mm hole, and seek a reliable component brand to complete the story with a suitable seatpost. This meant that the end user could replace the part with the best seatpost for them, at any time they wished.
As technology has developed, brands have sought gains via added compliance, improved aerodynamics and weight reduction. It’s no secret that the seatpost is pivotal in the compliance story, and that optimisations can have a significantly greater effect when compared with frame advancements. Ditto, with brands using CFD and wind tunnel testing to inform frame design, they can see exactly how many watts can be saved by smoothing out the relationship between the seatpost and the frame it sits in.
The result? Proprietary seatposts. Rather than rely on a third party to develop this component, the brand does the work itself - or - teams up with a component manufacturer to create a custom solution for this particular frame. For the manufacturer, this has the added benefit that the customer is now fully reliant on the brand for component updates in the future. The consumer might get a better overall package, but they are somewhat tied in - and some high-profile examples suggest that frame manufacturers don't always get it right.
Some internal cable routing
Going fully integrated looks neat, but...
Internal cable routing used to refer simply to cables that were internal from the downtube and top tube. This keeps muck out of the cables and cuts down on maintenance. Fully internal cables are completely hidden from view - very often travelling from the shifters into the handlebars, through the stem and headset and passing alongside the steerer tube to reach their destination. Every brand has its own method, some are better than others.
Routing cables in a manner that minics the worst of the London underground network can present issues.
Firstly, a headset change requires re-cabling, and multiple local bike shops tell us that what was once a five-minute procedure is now something they allow half a day for - at a substantial cost to the consumer.
Secondly, these systems involve new methods of engineering, and ‘new’ sometimes results in mistakes. Case in point, the recall on all Specialized SL7 frames, following concern that the compression ring which also acted as a guide for internal cable routing may put undue stress on the steerer and cause failure. The US Consumer Product Safety Commission (CPSC) website shows Specialized had only two cases of failure, following impact, and no injuries were reported. However, a fork steerer failure is not something anyone wants to experience and the brand was concerned enough to issue a stop ride notice to consumers - until replacement parts could be fitted.
Fork recalls are nothing new, unfortunately, but some systems used to hide away cables can become a contributing factor - as can the seemingly never-ending search for weight and aero savings.
Aero tubing on endurance and climbing bikes
Keeping tubing round, with a few nods to aero - like the TCR - has its benefits on ride quality
Ride quality is impacted by many factors: material choice, layup, the components fitted to the final product, and tube profile. Round tubes are responsive and lighter, but chunky, boxy tubes are more aerodynamic.
The prevailing voice within bicycle design states that aerodynamics have a greater impact upon overall speed, vs weight. This assertion comes from comparison data, and applies down to riders cycling at about 15mph/25kph - and below. Therefore, the direction of travel has been to optimise frames for aerodynamics. This approach is sensible, if speed is your primary goal. No sprinter wants to hand watt savings to rivals any more than they want to speak to dictaphone waving journalists seconds after losing the battle.
If, however, you’re more interested in how a bike feels to ride, then round tubes will maximise the fun factor. Sure, you can make the argument that endurance riders and climbers still want to go fast, and aero tubes will help them to do that - but do they want to go fast more than they want to have fun? Probably depends on their Strava settings.
Wheel rim/tyre incompatibilities
Tubeless = low pressure = better cornering, that's not under dispute - but compatibility is
First, we're not going full 'retro grouch'.
Tubeless tyres allow for lower pressures and wider tyres, which widen the contact patch and can vastly improve cornering prowess as well as reducing fatigue and losses via vibration on rutted road surfaces. This is not in dispute. High pressures are faster on glass smooth roads, but I've got a prize for anyone who can devise a local route made up of 50%+ of this magical tarmac of dreams. Once compatibility issues are addressed (and sealants are optimised for road pressures) we’ll be away. But there’s work to do yet.
Roadie tyre technology has changed in recent years, and the risk associated with failing to keep up ranges from providing your mate with a ‘sealant facial’ on a chain gang, spending an evening wrestling with a tyre that will not go on the rim (even when smothered in an entire bottle of Fairy Liquid and adorned with 30 tyre levers*), to being discovered in a ditch somewhere, a trail of white splatter acting as a roadmap to your location (beside the hookless rim and non-hookless compatible tyre combo you’ll later discover you over-inflated, by 200%+*).
The point here is that we are not at all against tubeless tech, and we're not against hookless tech, but we are in favour of greater standardisation - and communication - between the wheel and tyre brands.
* NB, please don't take this artistic license seriously and actually do any of these things
Price
It’s fair to say that the price of top end bikes has increased far in excess of inflation in recent years. Dura Ace, 50mm deep carbon rims, power meter, top end carbon frame, will probably set you back £10-11k. And the cost of production is definitely lower than the added RRP, there’s no doubting that.
Now, I do completely disagree with the “you could get a motorbike for that” argument. And that’s because these £10-11k bikes are UCI pro ready.
Yes, you could buy a Honda CBR650R for £7,729 and still have change left over to buy leathers and a fancy helmet over buying an £11,000 bicycle. But a few steps up the rungs and you'd need £20,000 for something track-ready like a Honda Fireblade SP. I can't see many Moto GP fans shelling out the $1 to $2.5 million they'd need to spend to ride a bike the same as their idols.
The reasons given for higher bike prices include the rising cost of production. Initially, brands had bikes produced in Asia because it was cheaper. But, unsurprisingly, countries in Asia have got really good at making bike frames, and that expertise now comes at a premium. Secondly, very few brands produce their own carbon (Giant is an exception). Many get carbon from the Japanese giant, Toray. Toray now offers a new carbon grade: Toray M40X. This is stiffer so allows for the use of less material which equals lower weight, but it also costs more to purchase.
So, rising labour costs, rising material costs, plus rising shipping costs after Covid, and Brexit in the UK. However, some of it is just the simple fact that consumers are shelling out five figures to own ‘the best’, so, brands will continue to charge that amount.
Endless bottom bracket standards
There's plenty of incentive to increase stiffness at the BB - but the maze of standards is too much
Who would have thought that the component which houses the crankset, facilitating the movement of the cranks and thus the forward propulsion of a bicycle, could require so many standards?
The area around the bottom bracket is critical to effective power transfer, and brands have experimented with many methods of “optimising” this junction in order to offer all manner of claimed benefits: more stiffness, less weight - and... more noise?!
At our last count, there were 21 bottom bracket standards, but it’s likely we’ve missed some (BBWrong?). T47 seems to be the new favourite at Trek, and carries some plausible recommendations: it’s compatible with a wide range of crankset diameters, carries the same dimensions as the PF30, but offers a threaded interface - aiding maintenance and (in theory) cutting creaks - which are largely a result of imperfect frames. But that’s no use to you, if, for example, you’re riding a Cervelo with a BBRight or a BB30 wearing Cannondale.
Perhaps what’s needed is some external governing body able to ultimately enforce convergence on one standard. But, of course, it’s most likely they’ll just end up swimming against the tide, and being slapped in the face by a wet salmon.
Thank you for reading 20 articles this month* Join now for unlimited access
Enjoy your first month for just £1 / $1 / €1
*Read 5 free articles per month without a subscription
Join now for unlimited access
Try first month for just £1 / $1 / €1
Get The Leadout Newsletter
The latest race content, interviews, features, reviews and expert buying guides, direct to your inbox!
Michelle Arthurs-Brennan the Editor of Cycling Weekly website. An NCTJ qualified traditional journalist by trade, Michelle began her career working for local newspapers. She's worked within the cycling industry since 2012, and joined the Cycling Weekly team in 2017, having previously been Editor at Total Women's Cycling. Prior to welcoming her first daughter in 2022, Michelle raced on the road, track, and in time trials, and still rides as much as she can - albeit a fair proportion indoors, for now.
Michelle is on maternity leave from April 2025 until spring 2026.
-
Entire Movistar team fined after start ramp chaos at Vuelta Femenina
Visma-Lease a Bike file official complaint with the UCI following team time trial delays
-
Cycling further or cycling faster, which is better for weight loss?
Long and slow or short, hard and fast. If your goal is to reduce body fat which of these methods will get the best result?